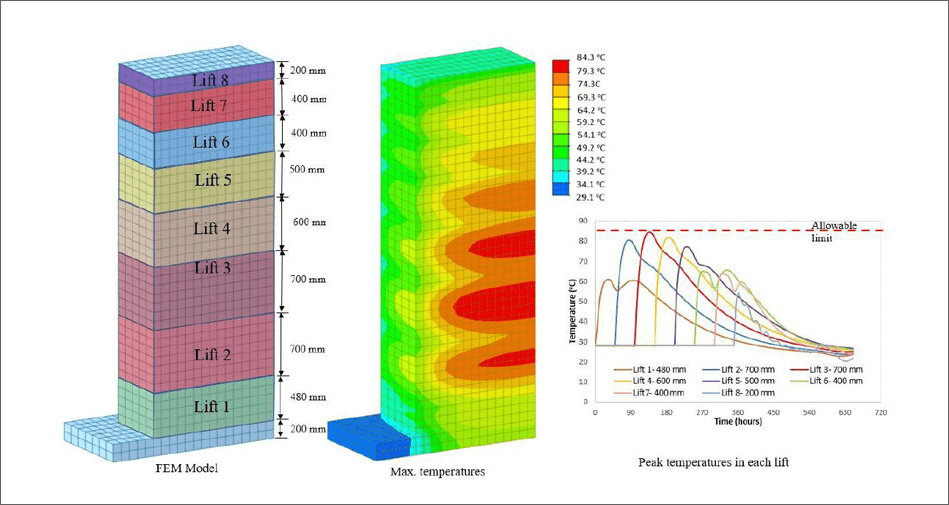
Thermal Modelling of Mass Concrete Elements
When constructing mass concrete elements, the long term durability of the concrete can be compromised if consideration is not given to limiting peak temperatures and temperature differentials within the concrete. To understand concrete temperature rise, thermal modelling is undertaken considering factors such as the concrete mix design, curing conditions, restraint factors, concrete geometry, tensile strain capacity, coefficient of thermal expansion and reinforcement spacing.
Thermal modelling is used to characterise the behaviour of the concrete during the curing and hardening phases. Limits are placed on concrete temperature rise and distribution to reduce the risk of cracking; as well as to control delayed ettringite formation (DEF). Crack modelling is undertaken to limit crack widths to within allowable code limits.
BCRC recently completed thermal and crack modelling in accordance with standards (such as CIRIA C660, CIRIA 766 and CIA Z7-06) for a transfer wall of a high rise residential complex.
The construction of the transfer wall was proposed to be undertaken in 6 layers with a variable thickness of the wall of 0.6m – 2.3m and a total wall height of 4m. This unique shape and construction sequence created a complex challenge.
FEA analysis was required as the thermal gradient from the lower sections added heat to the newly cast adjacent sections. This analysis could not have been satisfactorily completed using simple spreadsheets due to the complex nature of the project. Field temperatures were measured onsite during a trial pour and were used in the FEA analysis as heat inputs to allow for an accurate determination of the peak temperatures within the concrete.
From our analysis, it was determined that a pour sequence of 6 layers would result in an unacceptable risk to the concrete and therefore the pour sequence was modified to include 8 layers. The modelling process allowed BCRC to provide limits for the concrete placing temperature of the layers to eliminate the risk of DEF formation and to control thermal cracking to within allowable code limits.
The FEA output is provided below.