Materials and Construction
Our material engineers go to great lengths to specify performance and workmanship requirements for concrete but if the materials quality assurance and storage, concrete batching and transport, and placing, compaction, finishing and curing are not correctly undertaken it was all too no effect. For quality insitu concrete it is vital to follow the specification with appropriate sourcing, production and placing. BCRC can manage the whole process of achieving concrete fit for purpose.
Concrete Materials
BCRC provide specifications of water, sands, cements and aggregates suited to the exposure, design life and reliability required. We can also assess sources of supply and undertake test programs to validate new products and sources. No matter what the additional ingredient, fibres, admixtures or polymers BCRC can assure that the concrete produced will have appropriate properties and durability. Of course suitable materials also extends to construction and use of formwork, insulation, form oils and curing compounds.
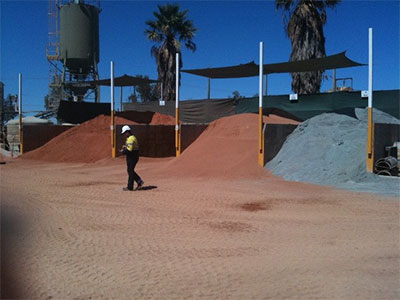
Concrete plant and materials assessment is a common BCRC assigment
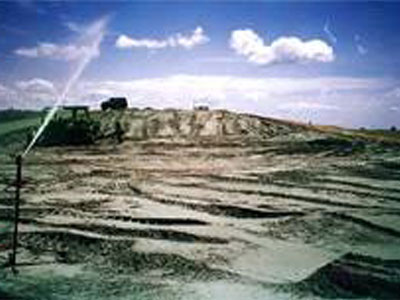
BCRC can advise fly ash collection and processing, directly or from stock piles
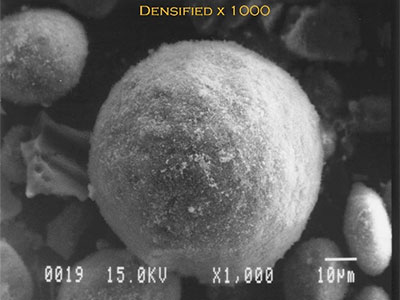
BCRC can assess materials, such as silica fume, either generally or form a specific plant
Making and Transporting Concrete
BCRC can access all types of concrete production plant
BCRC experts can provide advices on fibre mixes and handling mathods
Cheking truck mixers can be part of BCRC’s assessment of concrete supply
Placing, Compacting, Finishing and Curing
Mix design and curing were critical to achieving a 24th turnaround with no further curing
Shotcrete mix design and assessment of application are critical to performance
Curing is one of the most vital parts of achieving high performance cover
Why BCRC?
BCRC provides specialist consultancies in the following:
Concrete Applications | Concrete Materials | Making, Forming & Placing Concrete |
Air Entrained Concrete | Admixtures | Aggregate Sourcing |
Chemically Resistant Concrete | Alkali Activsators | Aggregate Crushing and Sizing |
Decorative Concrete | Cement | Batch Plants |
Deep Pours | Aggregate | Cement Manufacture |
Dropped Concrete | Light Weight | Extruded Concrete |
Ductile Concrete | Normal Weight | Formed Concrete |
Fire Resistant Concrete | Heavy Weight | Gunite |
Geopolymer Concrete | Fibres | Heat Cured |
High Strength Concrete | Synthetic | Premixed Concrete |
High Early Age Concrete | Steel | Preplaced Aggregate |
Lime Concrete | Fly ash floaters | Pumped Concrete |
Marine Concrete | Fly ash | Roller Compacted Concrete |
Mining | Glass | Sand Mining |
Pervious Concrete | Polymers | Self Compacting Concrete |
Postensioned Concrete | Polystyrene beads | Shotcrete |
Precast Concrete | Recycled Aggregate | Site Mixed Concrete |
Prestressed Concrete | Reinforcement | Skipped Concrete |
Resilient Concrete | Rubber | Slip Formed Concrete |
Salt Scaling Resistance | Sand | Steam cured |
Slabs | Silica fume | Transport Concrete |
Sustainability | Slag | Tremied Concrete |
Tall Pours | Void Formers | Unformed Concrete |
Underwater Concrete | Water | Volume Mixed Concrete |
Research and Innovation in Concrete
Air Entrained Concrete – Air entrainers are used to make up for deficiency in sand. The air bubbles created are fine (smaller than entrapped air) and act like fine ball bearings to help lubricate the mix without the effect other fines have on water demand. In some concrete application excessive use particularly can have negative effects, e.g. giving rise to blisters and delaminations is burnished finishes. BCRC can advise when, and when not, to use air entrainers and how their use should be monitored.
Chemically Resistant Concrete – Common forms of attack or sulphates, acids and biological agents. BCRC understand how to mitigate their effects on concrete and how to design the structure for resistance for the effects. There are also a wide range of chemicals that can attack concrete and it is not always apparent what a proprietary item may contain. BCRC can provide advice on the aggressivity of chemicals and how concrete resistance to deterioration can be improved.
Decorative Concrete – Making and placing concrete so that it is attractive rather than a dull, bland and cracked finish requires attention to mix design, finishing, placing, curing and post working. A misstep at any point can lead to a finish that does not meet the initial expectation. BCRC can advise on what is achievable, what the effect is on performance, how to specify and supervise to ensure satisfactory performance.
Deep Foundations – The development of concrete for use in deep foundations is particularly critical. If an appropriate mix is not developed, and proven by rigorous testing, then the piles barrettes or diaphragm walls can be found to have extensive voidage. In water retaining cases this leads to severe leakage. The costs of delays and repairs can far exceed the original construction cost. BCRC can help develop appropriate mix development and trials, establish ongoing QA requirements for structures to be built. Where problems have occurred they can advise on the root cause, durability issues and repairs required.
Dropped Concrete – 2m is often quoted as the limit for dropped concrete. The concern is segregation. However much deep drops have been successfully undertaken using appropriate mixes and techniques. Very deep drop application are most frequent in mining but drops of several meters may make construction much simpler in many infrastructure and building applications. BCRC can help develop and test mixes for deep drops
Ductile Concrete – Fire Resistant Concrete – Passive Fire-Resistant materials are often applied without sufficient consideration of detailing and quality assurance. While the concrete materials may be satisfactory failures can occur leading to severe consequences. Delamination in PFP in overhead situations for example might prejudice operation of the structure. BCRC can provide guidance on the design, application and testing of PFP from a structural perspective.
Geopolymer Concrete – In many cases geopolymers provide a sustainable advantage over concrete but they can also provide performance enhancements such as acid resistance. There may also be negative performance aspects. BCRC directors have been involved at the forefront of assessment of geopolymer mixes and can assist in developing of mixes for specific applications
- High Strength Concrete
- High Early Age Concrete
- Lime Concrete
- Marine Concrete
- Mining
Pervious Concrete: – Pervious concrete allows the passage of water and is useful to prevent flooding or more generally to assist drainage. Either for small or large areas concrete driving, parking or storage areas can be established that do not flood even where drainage systems are lacking. We can advise on mix design and develop mixes for different levels of permeability by controlling the concrete structure by varying the fines content.
- Piles
- Postensioned Concrete
- Precast Concrete
- Prestressed Concrete
Resilient Concrete – While concrete can be designed to withstand design loads extreme events may cause failures for which there is no practical repair. Resilient concrete is designed so that in the event of extreme events that cause failure the concrete will be left in a repairable condition. BCRC can work with designers to develop concrete and reinforcement will achieve this.
- Salt Scaling
- Slabs
- Sustainability
- Tall Pours
- Underwater Concrete